7.10.3 Hints on Pipeline Design 36 7.10.4 Pipe Combination 36 7.10.5 Joining of Pipelines 37 7.11. 2.4 Construction of Catchment for a Gravity Spring 52 2.4.1 Excavation 53 2.4.2 Design and Construction of Catchment 54 2.4.2.1 Barrage (Dam) 54. Construction and Standardisation of Gravity Water Supply Systems in Rural Villages. Operation and Maintenance of a Small Drinking-water Supply iii Contents 1 Introduction 1 1.1 What this booklet covers 1 1.2 Further guidance 1 2 Setting Objectives for the Operation of Your Water Supply 2 2.1 Quantity and pressure 2 2.2 Quality 3 2.3 Cost 3 2.4 Other level-of-service targets 3 2.5 Recording performance 4. 2.1 water demand 8 2.2 water distribution systems 10 2.3 water distribution modeling 11 2.4 pumps 13 2.5 valves 17 2.6 tanks and reservoirs 18 2.7 controls devices 19 2.8 epa 20 3.0 laying out a project 21 3.1 existing data 22 3.2 schematic generally 22 3.3 pressure zones 23. Including water mains 54-inch diameter and smaller and all sizes of gravity and pressure sewers with the exception of privately owned and maintained systems referred to as 'on-site' systems. It is the WSSC's policy to avoid and protect environmentally sensitive areas wherever possible.
Our ‘Step-by-step’ blog series takes a look at different practices and procedures in the transmission pipeline industry.
This week we’re outlining what happens during the pipeline design process – it’s more involved than you might think! Based on over 500 pages of standards and regulations, the design for each pipeline covers every aspect from routing, materials, pipe construction, laying the pipeline, safety and pipeline integrity.
Here’s a quick look into the world of pipeline design
Pipeline design begins with a study of the proposed route, including full environmental and engineering assessments:
Designers draft detailed schematics based on over 500 pages of standards:
The composition of the steel is a key factor to in the pipeline’s integrity. That’s why alloys may be added to the steel so it meets the precise specifications:
Pipeline Inspection
Pipelines are inspected using X-ray technology and hydrostatic testing. This technician is inspecting the pipe from the inside!
The pipeline is then coated with corrosion-resistant, powdered epoxy:
During construction, huge valves are placed along the pipelines at regular intervals so the flow can be shut off in the event of a spill:
After construction, the land is remediated. Aside from above-ground facilities at intervals along the pipe, there is almost no sign that the land has been disturbed:
Of course that’s the shortened version of the process! If you’d like to learn more, watch this video for the full story:
Stay tuned as we continue this ‘Step-by-step’ series. Next we’ll take a look at pipeline technology. In the meantime, if you’d like to learn more about pipeline design, check out this blog post: Pipelines: safe by design.
The Canadian Energy Pipeline Association represents Canada’s transmission pipeline companies who operate approximately 117,000 kilometres of pipelines in Canada. In 2014, these energy highways moved approximately 1.2 billion barrels of liquid petroleum products and 5.4 trillion cubic feet of natural gas. Our members transport 97 per cent of Canada’s daily natural gas and onshore crude oil from producing regions to markets throughout North America.
Explore CEPA
Get Connected
Engage in the online discussion
Numerical Example
Figure 22 below shows the topographic survey results for a proposed gravity flow water system.
Assuming that the allowable pipe pressure head is 100m, the safe yield from the spring is 0.25LPS and that the design parameters from Jordan are adhered to (see Appendix 4.), design a system that will supply water to the community for the minimum cost.

Answer
The design of this water system will be approached in the following phases: Zune software for windows 10.
- Requirement for and placement of break pressure tanks.
- Design of pipe work.
- Check chosen pipe work for low pressure head parameter.
1. Requirement for and placement of break pressure tanks
Consider the control valve at the reservoir tank being closed to begin with. This is the maximum static head condition (Appendix 4 No. 1). All the static heads can be calculated from Equation (35)below:
Consider the section of the system from the spring (point 1) to low point 2. The static head is:
which exceeds the 100m allowable pipe pressure head given above.
Consider the section of the system from the spring (point 1) to high point 3. The static head is:
which is within the above limit.
Consider the section of the system from the high point 3 to the reservoir tank (point 4). The static head is:
which exceeds the 100m allowable pipe pressure head given above.
It is clear that the pipes at points 2 and 4 will blow unless we introduce break pressure tanks to relieve the pressure.
The first break pressure tank (hereafter BP1) must relieve the pressure at point 2 but still allow the water to flow over point 3.
The maximum height (hBP1) we can place BP1 at is given by:
so:
and therefore:
and:
so:
and therefore:
So the height of BP1 must be less than or equal to 150 and greater than 125, to satisfy the conditions. As there will be frictional losses in the pipes we should situate BP1 at its maximum allowable height, which is in this case 150m. This corresponds to a location approximately 225m from the spring tank.
The second break pressure tank (hereafter BP2) must relieve the pressure at point 4 but not exceed the pressure head limits in the pipe work between it and BP1.
The maximum height (hBP2) we can place BP2 at is given by:
so:
and therefore:
And
so:
and therefore:
So the height of BP1 must be greater than or equal to 50 and less than or equal to 100, to satisfy the conditions. So it will be placed at a height of 70m. This corresponds to a location approximately 2500m from the reservoir tank.
The two break pressure tank locations are added to the topographic survey, and shown below in Figure 23.
Figure 23
y inspection of Figure 23, the maximum static heads (after the introduction of the two break pressure tanks) are as follows:
At BP1:
At Point 2:
At Point 3:
At BP2:
At Point 4:
All of which are acceptable.
2. Design of pipe work
The safe yield of the water source is 0.25LPS. So in general we want to make sure that at no point in the system is more than 0.25LPS being drawn, as this will either empty a break pressure tank or the spring tank, allowing air into the system. We can do this in two ways.
- Design the natural flow situations such that just less than 0.25LPS is being drawn.
- Use control valves at the break pressure tanks and reservoir tank to limit the flow to just less than 0.25LPS.
We will consider the second option because the calculations are simpler and the control of the system easier.
Consider the section of pipe between the spring tank (point 1) and BP1:
This section of pipe is 225m long and the maximum static head is 50m (see above). From the friction tables for a controlled flow of 0.25LPS we get the following data.
Pipe Diameter | Frictional head loss (m/100m) | Frictional head loss for 225m of pipe (m) | Velocity (m/s) |
---|---|---|---|
½” | 13.61 | 30.62 | 1.28 |
¾ “ | 3.47 | 7.81 | 0.73 |
1″ | 1.07 | 2.41 | 0.45 |
1¼ “ | 0.28 | 0.63 | 0.26 |
It is clear that we can use ½” dia. pipe here, as it will not reduce the maximum static head below the 10m low pressure head limit (see Appendix 4. No. 3) and the velocity of the water lies within acceptable parameters (see Appendix 4 No. 4).
The residual head at the BP1 valve (ΔHBP1) is given by Equation (34):
Substituting the numerical values into this equation for ½” dia. pipe we get:
This is an acceptable residual head based upon the limits set in Appendix 4 No. 6.
Consider the section of pipe between BP1 and BP2:
This section of pipe is 2500 – 225 = 2375m long. The main feature we have to contend with is the topographical peak at point 3. This only lies 25m below BP1, so we can’t afford to “burn off” too much frictional head between BP1 and point 3 or else the residual head will drop below the limit of 10m (see Appendix 4. No. 3). So we need to burn off no more than 25 – 10 = 15m of head between BP1 and point 3.
The distance between BP1 and point 3 is from Figure 23, 1800 – 225 = 1575m. From the friction tables for a controlled flow of 0.25LPS we get the following data.
Pipe diameter | Frictional head loss (m/100m) | Frictional head loss for 1575m of pipe (m) | Velocity (m/s) |
---|---|---|---|
½” | 13.61 | 214.36 | 1.28 |
¾ “ | 3.47 | 54.65 | 0.73 |
1″ | 1.07 | 16.85 | 0.45 |
1¼ “ | 0.28 | 4.41 | 0.26 |
We clearly cannot use ½” and ¾” diameter pipes here as they “burn off” far more than 15m of head.
We could use 1¼ ” dia. pipe here, but there are two problems. Firstly the water velocity is very low at 0.26 m/s (see Appendix 4 No. 4) and secondly it is a little more costly than 1″ dia. pipe (Appendix 4 No. 8).
So consider using 1″ dia. pipe. The water velocity is still below the limit of 0.7 m/s (see Appendix 4 No. 4), but the head loss is almost acceptable. There seems to be only one solution. Use 1″ pipe between BP1 and point 3, and place a wash out at the lowest point between BP1 and point 3, which happens to be point 2.
The pressure head at point 3 (H3) is given by Equation (34):
Substituting the numerical values into this equation for 1″ dia. pipe we get :
This is a little less than the minimum low pressure head limit of 10m (see Appendix 4 No. 3) but is acceptable in the circumstances.
Now consider the second section of pipe between point 3 and BP2. The remaining pressure head is 8.15m (from above) and so we can add this to the remaining head between point 3 and BP2 to get the overall head.
The most desirable residual head (Appendix 4 No.6) at a valve or tap is around 15m. So we are looking to “burn off” something like :
The distance between point 3 and BP2 is from Figure 23, 2500 – 1800 = 700m. From the friction tables for a controlled flow of 0.25LPS we get the following data.
Pipe diameter | Frictional head loss (m/100m) | Frictional head loss for 700m of pipe (m) | Velocity (m/s) |
---|---|---|---|
½” | 13.61 | 95.27 | 1.28 |
¾ “ | 3.47 | 24.29 | 0.73 |
1″ | 1.07 | 7.49 | 0.45 |
1¼ “ | 0.28 | 1.96 | 0.26 |
We clearly cannot use ½” diameter pipe here as it “burns off” far more than 48.15m of head.

2.4 Gravity Pipeline Design Water Supply System Definition
¾ ” dia. pipe here looks good, as although it only burns off approximately half of the required head, it produces a water velocity within the parameters required (Appendix 4 No. 4) and is cheaper than the 1″ dia. pipe (Appendix 4 No. 8).
The residual head at the BP2 valve (ΔHBP2) is given by :
2.4 Gravity Pipeline Design Water Supply System
Substituting the numerical values into this equation for ¾ ” dia. pipe we get :
This is in the high end of the residual head range based upon the limits set in Appendix 4 No. 6.
We can improve on this and reduce costs by using a combination of ¾” dia. pipe and ½” dia. pipe. Consider the combination pipes Equation (41).
Where:
X = Length of smaller diameter pipe, to give desired frictional head loss (m).
H = Desired frictional head loss (m).
fhl = Frictional head loss due to larger diameter pipe (m/100m).
fhs = Frictional head loss due to smaller diameter pipe (m/100m).
L = Total length of pipe (m).
In this case our desired head loss (H) is 48.15m, L = 700m, fhl = 3.47m/100m and fhs = 13.61m/100m (from above), so :
This close to 200m, and as the pipe usually comes in 100m lengths, we should employ 200m of ½” dia. pipe and 500m of ¾ ” dia. pipe.
This combination of pipes will produce a total frictional head loss (fhcomb) of :
So the residual head at the BP2 control valve will be :
This very close to the desired residual head based upon the limits set in Appendix 4 No. 6.
Consider the section of pipe between BP2 and the reservoir tank (point 4) :
This section of pipe is 3200 – 2500 = 700m long and the maximum static head is at point 4 and is 70m (see above). From the friction tables for a controlled flow of 0.25LPS we get the following data.
Pipe diameter | Frictional head loss (m/100m) | Frictional head loss for 700m of pipe (m) | Velocity (m/s) |
---|---|---|---|
½” | 13.61 | 95.27 | 1.28 |
¾ “ | 3.47 | 24.29 | 0.73 |
1″ | 1.07 | 7.49 | 0.45 |
1¼ “ | 0.28 | 1.96 | 0.26 |
If we try to achieve the desired residual head at the reservoir tank valve of 15m (see Appendix 4 No. 6) then we need to “burn off” 70 – 15 = 55m of head through friction. Studying the data above suggests that a combination of ½” and ¾ ” pipe would be the optimum solution. Using the combination pipes Equation (41) as previously:
In this case our desired head loss (H) is 55 m, L = 700m, fhl = 3.47m/100m and fhs = 13.61m/100m (from above), so:
This close to 300m, and as the pipe usually comes in 100m lengths, we should employ 300m of ½” dia. pipe and 400m of ¾” dia. pipe.
This combination of pipes will produce a total frictional head loss of :
The residual head at the reservoir tank control valve (ΔH4) is given by equation (34) :
Substituting the numerical values into this equation for the combination of ½” dia. and ¾ ” dia. pipe we get:
This is an acceptable residual head based upon the limits set in Appendix 4 No. 6.
3. Check chosen pipe work for low pressure head parameter
At this stage of the design we need to check that we have not reduced the pressure head in the pipe below the 10m limit set in Appendix 4 No. 3. We can do this most simply by plotting the Hydraulic Grade Line (see Jordan) onto the topographic survey. To do this we need to tabulate all the chosen pipe sections, their lengths and their respective friction head losses based upon a controlled flow of 0.25LPS. This data is shown below:
Section | Pipe dia. | Length (m) | Frictional head loss (m/100m) | Total frictional head loss (m/100m) |
---|---|---|---|---|
1–BP1 | ½” | 225 | 13.61 | 30.62 |
BP1–3 | 1″ | 1575 | 1.07 | 16.85 |
3–BP2 | ¾” | 500 | 3.47 | 17.35 |
3–BP2 | ½” | 200 | 13.61 | 27.22 |
BP2-4 | ¾” | 400 | 3.47 | 13.88 |
BP2-4 | ½” | 300 | 13.61 | 40.83 |
These lines are plotted onto the topographic survey as shown in Figure 24.
Examination of the HGL shows that it the pressure head never becomes negative (i.e. the HGL never goes below the ground surface) and its minimum is at point 3, which we have already considered. Therefore the chosen pipe work design is acceptable.
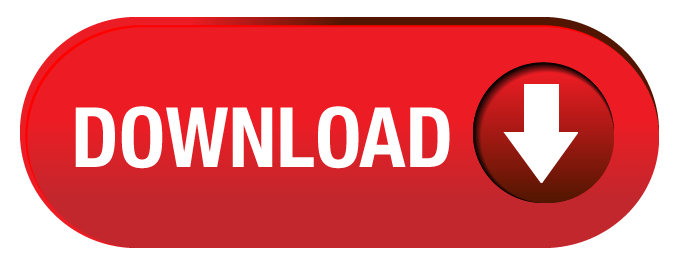